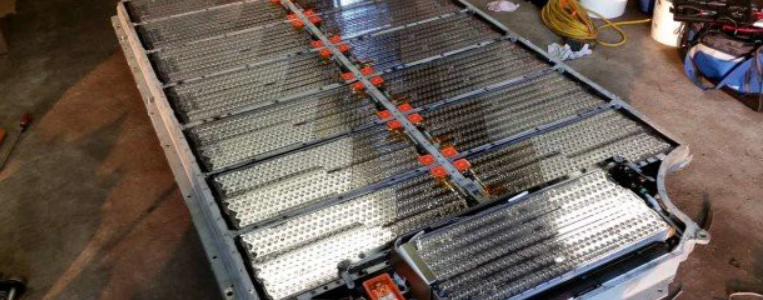
The Future of electric batteries recycling
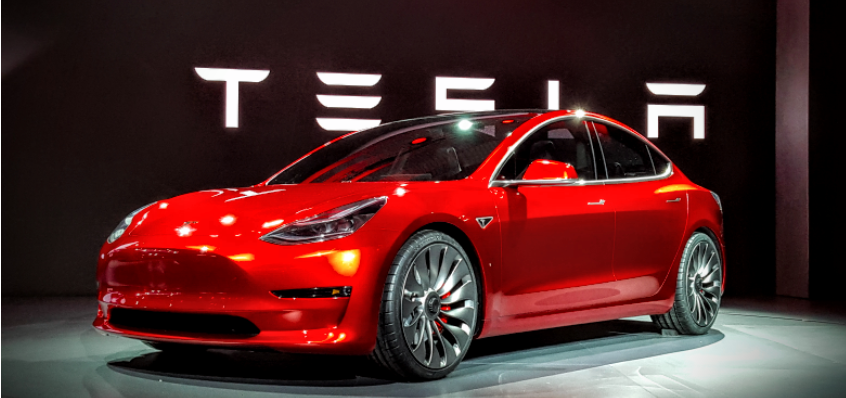
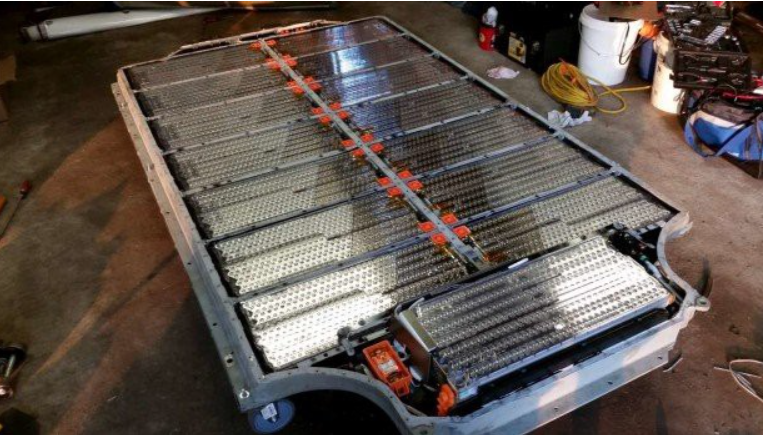
It is predicted by 2030, there will be 20 million electric cars on European roads alone. While Electric vehicles may be carbon neutral during their working lifetime, what happens when they run out of the road. In 10 to 15 years when there are large numbers coming to the end of their life it is going to be very important that we have a recycling industry, can Lithium-ion batteries be economically recycled.
EV batteries are larger and heavier than those used in regular cars and made up of several hundred individual lithium-ion cells, all of which need dismantling and contain hazardous materials, and also have a tendency to explode.
Nissan and Volkswagen are now reusing old batteries from their leaf cars in the automated guided vehicles that deliver parts to workers in their factories.
Thomas Tiedje, head of planning for recycling at Volkswagen Group Components in Salzgitter, Germany said “ We focus on cathode metals like cobalt, nickel, lithium, and manganese for recycling. Dismantled parts of the battery systems like aluminum and copper are given into established recycling streams.”
Renault is recycling all its electric car batteries with French Waste management company Veolia and Belgian chemical firm Solvay according to Jean-Philippe Hermine, Renault’s vice president for strategic environmental planning.
Tesla’s CTO JB Straubel after visiting the Fremont factory during UWA MBA Silicon Valley Study Tour and seeing our robot overlords ( including Wolverine) in 2018 said “We have current partner companies on every major continent where we have cars operating that we work with to do this today and in addition, we are internally developing more processes and we are doing R&D on how we can improve this recycling process to get more of the active materials back, and ultimately close the loop right at the Gigafactory that reuses the same recycled materials.”
Tesla’s batteries primarily manufactured in Japan and complaint to strict environmental laws (RoHS standards. The batteries are mostly made from lithium metal oxides and the anode from graphite, the electrolyte from lithium salts and the cathode from lithium, nickel, cobalt and aluminium, although they contain some lead, mercury and cadmium, hexavalent chromium, PBBs and PBDEs.
Tesla’s average batteries last up to 168, 000 miles ( 270, 000km) and Tesla Model S 90D nicknamed eHawk has been in service since 2015 and clocked up an astounding 400, 000 miles ( 643, 737km) really means the sky is the limit. The truth is no one really knows the end of battery life estimate for Tesla lithium-ion batteries, knowing that Tesla is a serious innovator, in fact, it places this as a competitive advantage over other car companies will reach greater efficiencies in their Gigafactory recycling processes.
Tesla battery weighs approximately 1000 lbs ( 454kgs) is far easier to apply recycling processes to it.
In the future, it may be possible to simply drive to your local Tesla service center and in a matter of minutes, your entire battery tray is replaced with brand new batteries with Tesla putting the old batteries through their recycling program, which Tesla patented the idea in 2017.
Tesla battery with electronics removed, tested, and reused, wires and metals are recycled locally, with large sums of electronics modules sent off o the Toxco materials management center.
Lithium modules are frozen with liquid nitrogen to prevent further chemical reactions. and later shredded into tiny pieces for further screening and separation into fluff, cobalt, copper, and slurry. Copper and cobalt are sold to recovery centers to be broken down into cobalt, nickel, copper, and aluminum. The slurry is reused for appliance coatings. Propylene Glycol is recycled locally after it is removed from the cooling tubes.
Tesla has chosen to work with Umicore for the European operations with 5 per cent of the global man-made CO₂ emissions worldwide being produced by cement manufacturing, Umicore replaces this raw construction material with secondary material, avoiding thermal processing and reducing CO₂ emission and non-renewable resource consumption.